1. Sorting and Cleaning:
After the food service trays from large school districts and corporate cafeterias arrive at plants they are placed on conveyer belts and manually sorted. Non – polystyrene items are removed from the line. Sorters are trained in proper procedures to eliminate any non-food adjutants or contaminants.
Foam trays are chopped and ground into 3 inch chips or flakes, then washed at 180 degrees to remove food contaminants, prior to being dried in a machine dryer.
2. Pelletizing:
The clean 3 inch flake is further reduced to ¼ inch nominal size and undergoes thermal densification to melt the polystyrene. The temperature reaches 400 degrees in the extruder and decreases the volume to weight ratio drastically. Then, the contents are then cooled into hard plastic pellets, about the size of a pea. EPG frequently tests pellets and inspects facilities to ensure that both are in compliance with agreements, specifications, and sanitization standards of the FDA.
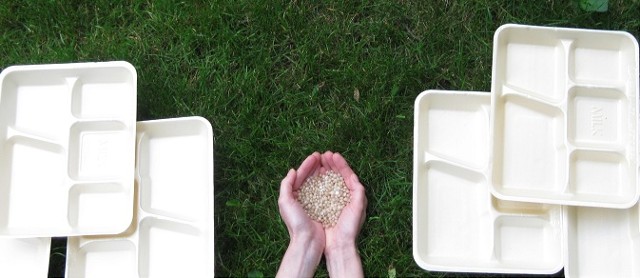